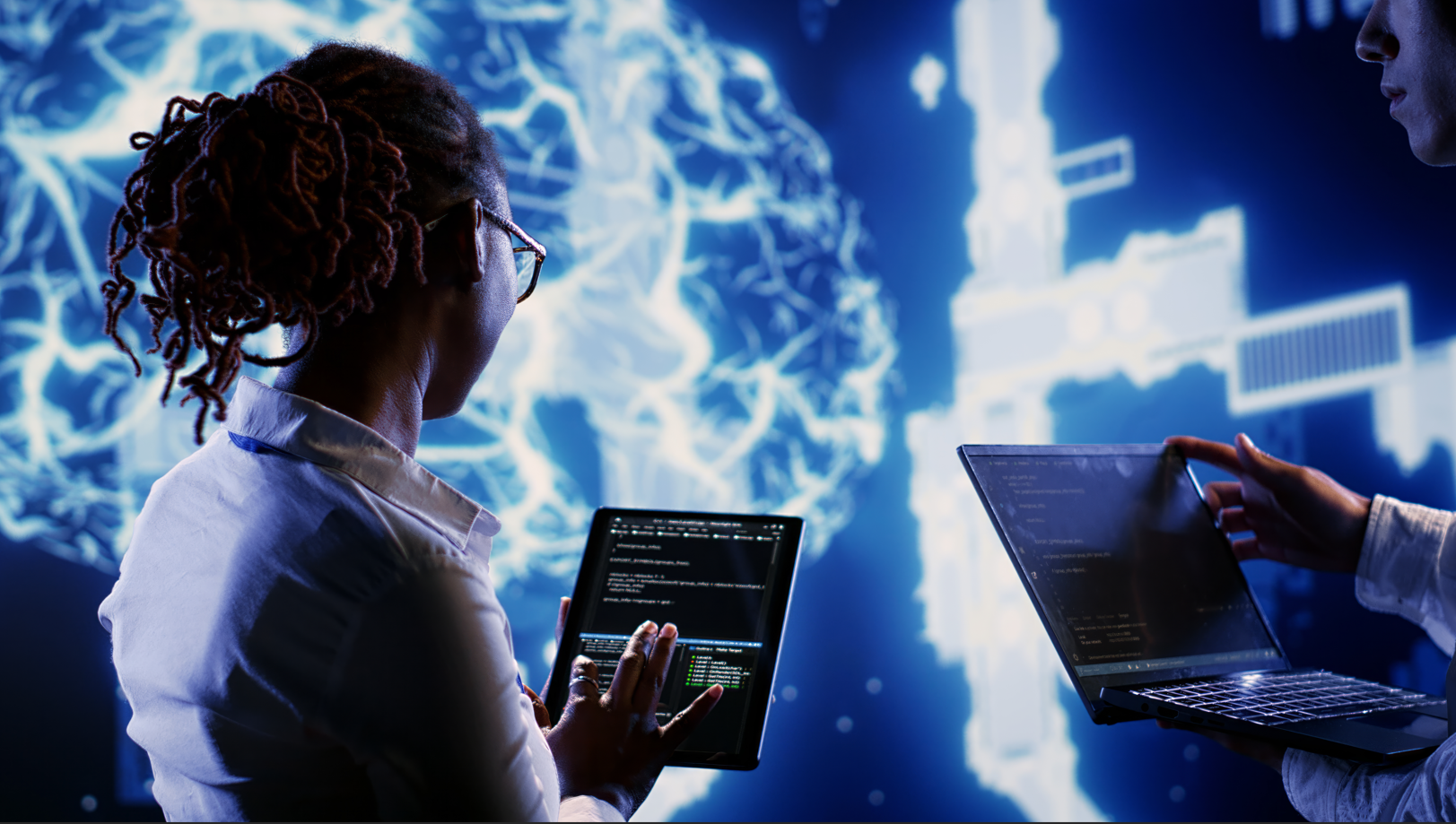
Un sujet majeur dans l’industrie : la maintenance prédictive
C’est l’un des sujets les plus importants aujourd’hui, dans l’industrie : avec la maintenance prédictive, les entreprises se dotent d’un monitoring précis des performances et de la durabilité des équipements essentiels de leur ligne de production. L’enjeu économique et technologique a fait de ce concept un sujet majeur dans le domaine de l’IT appliquée. FOCUS :
Le concept de maintenance prédictive
Maintenance anticipée, maintenance prévisionnelle… Plusieurs termes désignent un même concept très présent dans l’industrie d’aujourd’hui : la maintenance prédictive. Il consiste à effectuer une réparation sur une pièce non pas en fonction d’une panne présente, mais à la faveur d’une analyse poussée de multiples paramètres, dont la durée d’usure, les dégradations régulières, les contraintes… Et de réaliser une réparation préventive plutôt que curative.
Pour affiner ce concept, un certain nombre de KPI ont été intégrés dans les processus industriels. On va ainsi parler de MTBF, pour mean time between failure, soit le temps moyen entre deux pannes d’une pièce, de MTTF, pour mean time to failure, désignant la durée de bon fonctionnement, de MUT (mean up time, durée moyenne de fonctionnement après réparation) ou encore de MTTR (mean time to repair, temps nécessaire pour une réparation). Ces données, liées entre elles, permettent d’établir le moment optimal de la réparation, avant que la panne n’oblige le retrait de la pièce d’une ligne de production. Elles nourrissent un autre KPI, le TRS, soit le taux de rendement synthétique qui donne pour chaque équipement le nombre de pannes rencontrées et le temps passé en réparation.
Avec ces données, et un historique poussé, chaque secteur industriel démontre l’intérêt de la maintenance prédictive. En témoigne le domaine des transports, avec de nombreux équipements maintenus en fonction de ces KPI dans l’aviation, ou la sortie de pièces avec toujours de meilleurs ratios MTBF dans l’industrie ferroviaire, par exemple. Dans l’industrie manufacturière, la maintenance prédictive est particulièrement visible du côté des machines-outils et de leurs principaux composants.
Les enjeux de la maintenance prédictive
La prévention plutôt que la guérison : tel pourrait être le mot d’ordre de la maintenance prédictive, dont le principal enjeu est le gain de temps. En effet, pouvoir organiser la mise hors ligne d’un équipement et sa réparation, avec un calendrier optimisé pour la durée de vie de la pièce, s’avère beaucoup moins chronophage que d’attendre les étapes de diagnostics et de réparation.
À cette économie de fonctionnement basée sur le temps s’ajoute une véritable manne pour les entreprises industrielles, puisque le cabinet McKinsey chiffre à 630 milliards de dollars l’économie réalisée dans le monde en 2025 par les entreprises utilisant la maintenance prédictive. Ces économies sont réalisées grâce à une réduction des coûts de maintenance, devenant préventive plutôt que curative, par le réemploi de machine réparée plutôt que remplacée, et en dernière instance par une baisse du nombre de pannes.
Dans un monde enfin dont on connaît les limites en matière de ressources naturelles et de minerais, prolonger la vie d’un équipement industriel s’avère également un enjeu de taille. Aussi, la conservation avec réparation anticipée, plutôt que le remplacement à neuf, contribue à limiter l’impact carbone des entreprises concernées.
Les technologies IT sur lesquelles s’acculturer côté maintenance prédictive
La maintenance prédictive est devenue de plus en plus précise à mesure que des outils informatiques automatisés ont secondé les calculs manuels et les statistiques des fabricants d’équipement. Trois domaines sont directement utilisés par les industriels : le machine learning, la virtualisation et les data science.
Dans ce dernier domaine, la mise au point de calendrier de maintenance anticipée est accompagnée par la collecte de datas directement sur les lieux de production. Via des capteurs IoT pouvant mesurer performances, vibrations, températures sur la ligne de production, les entreprises ont accès à un grand nombre de chiffres bruts correspondant à autant de situations différentes. Chaque paramètre physique d’un équipement est scruté, suivant la durée d’utilisation et l’intensité, ce qui aboutit à nourrir une database pouvant être structurée en SQL et exploré avec des langages comme R, un outil assez puissant pour prédire les variations éventuelles.
Les données source peuvent être également intégrées à une simulation virtuelle (un « digital twin ») de l’équipement. De cette façon, les tests et les pannes éventuelles peuvent être accélérés de manière à établir un modèle précis pour chaque équipement. Cette approche utilise des structures de développement comme Matlab avec son environnement Simulink ou Modelica afin d’intégrer les propriétés physiques à une copie virtuelle entièrement paramétrable.
Dernière avancée en date, et non des moindres : le machine learning. En parvenant à lire les données brutes et à s’intégrer dans une ligne de production, un modèle entraîné autour d’un même équipement permet de déterminer un algorithme réaliste de fonctionnement avant panne. Différentes logiques peuvent être inculquées au programme d’apprentissage de maintenance prédictive (arbre de décision, forêts aléatoires, ensemble learning) afin d’affiner davantage l’exploitation des données et de préciser les résultats.
En ce sens, la maintenance assistée par ordinateur connaît actuellement sa révolution : les outils informatiques automatisés aident les organisations à se saisir de ces enjeux et à améliorer leur workflow industriel.
Chez agap2IT, nous mettons notre expertise au service de projets intégrant la maintenance prédictive pour répondre aux défis industriels de demain. Grâce à nos compétences en data science, IoT et intelligence artificielle, nous accompagnons nos clients dans l’optimisation de leurs équipements et de leur performance.